Developed to meet your need for affordable lightweighting
Developed by Tata Steel for the automotive industry, HyperForm grades are significantly more formable than their standard equivalents.
The enhanced formability enables robust processing and can improve press shop yield. It also enables the design of more complex shapes. The optimised stretchability of the HyperForm product range allows the replacement of conventional HSS and enables affordable lightweighting compared to standard AHSS/UHSS grades.
HyperForm's advantages for vehicle designers:
- More design freedom in part shape due to its extra formability
- Cost effective weight saving through upgrade and down gauging possibilities
HyperForm's advantages in production:
- Offers problem-solving solutions for the press shops 'most difficult-to-run parts
- Extra formability gives more options for addressing springback issues
- Very lean chemistry ensures excellent spot weldability
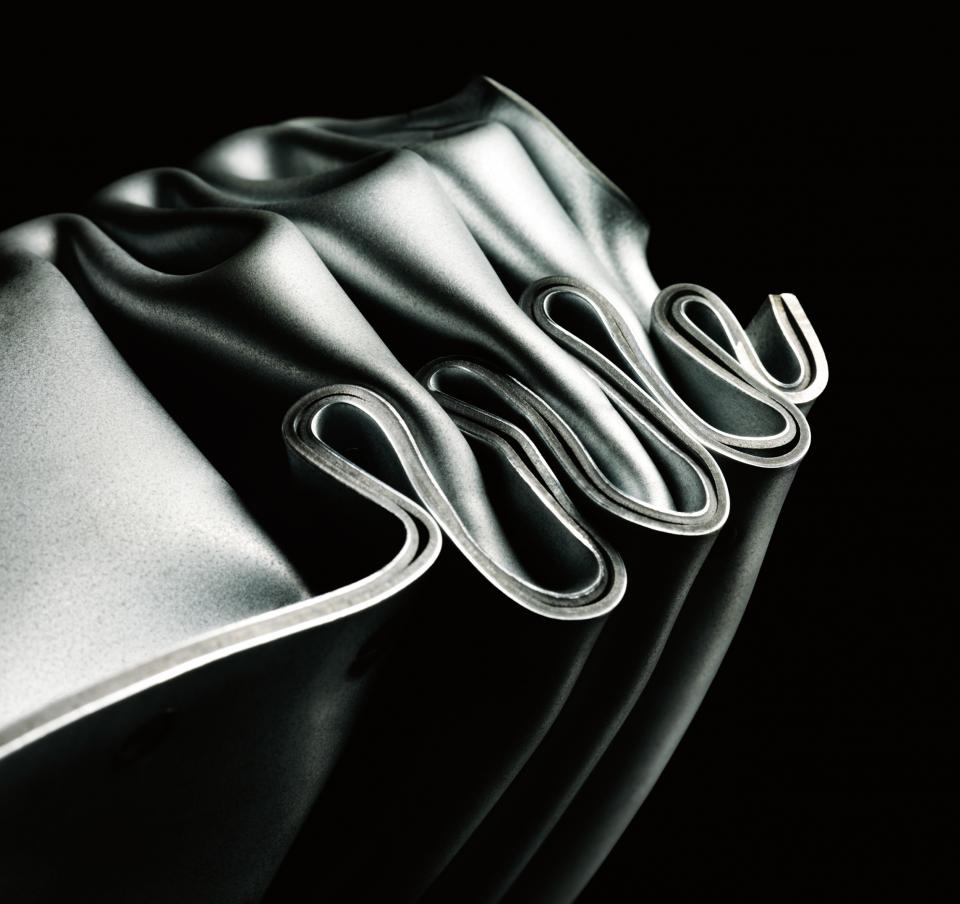
Extra formable HyperForm® steels combine the benefits of press shop efficiency with AHSS lightweighting
With elongation levels 4% higher than their standard equivalents, AHSS HyperForm grades offer superior formability. This delivers improved press shop efficiency and allows the lightweighting of complex, structural and crash-resistant components.
Meeting VDA 239-100 requirements
HyperForm products can be found within the AHSS product range and meet the requirements of the VDA239-100 norm as described in the ‘DH’ range. This paves the way for a broader application of these materials in the entire body-in-white design.
The HyperForm portfolio includes CR-DP800-GI HyperForm (or CR440Y780T-DH). The HyperForm range is recently being extended with a DP600-GI HyperForm.
Our material experts are there to support the deployment of our products in your specific application area. For more information contact our HyperForm experts.
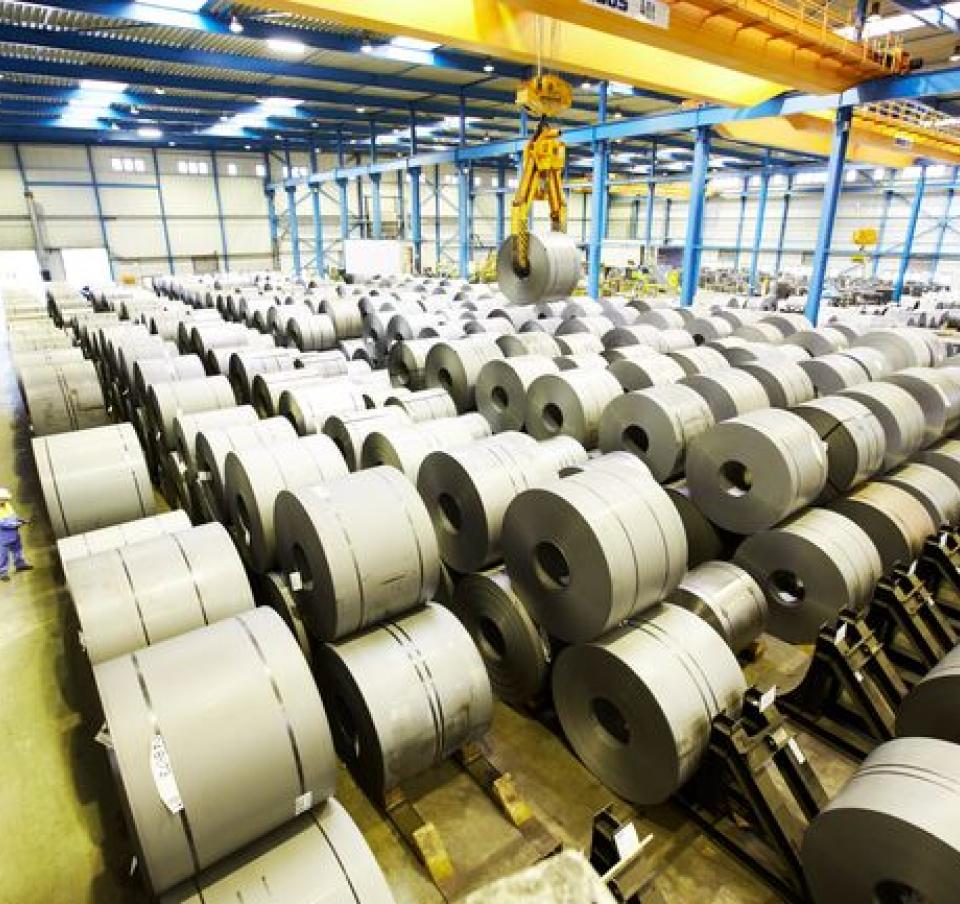
Looking for better weldability to lower your total cost of ownership?
The excellent welding performance of DP800-GI HyperForm is equivalent to that of DP800 -and better than TRIP800- due to a combination of relatively low carbon, phosphorous and sulphur content. Thanks to the controlled alloy additions, a typical weld window of 1.3kA is achieved using the VDEh welding procedure (SEP1220-2).
With special measurement techniques that have minimal impact on production activity our experts can quantify the effect on your total cost of ownership.
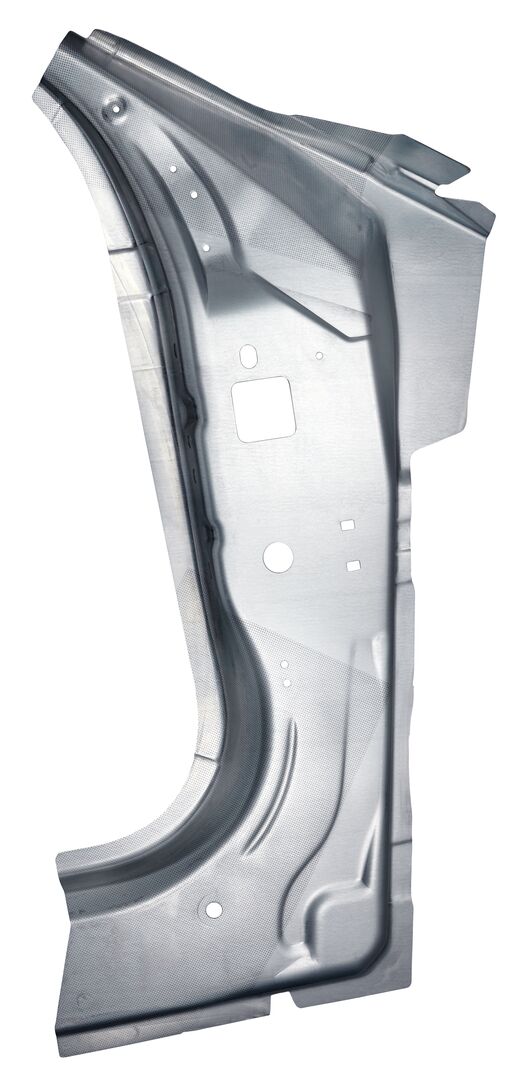
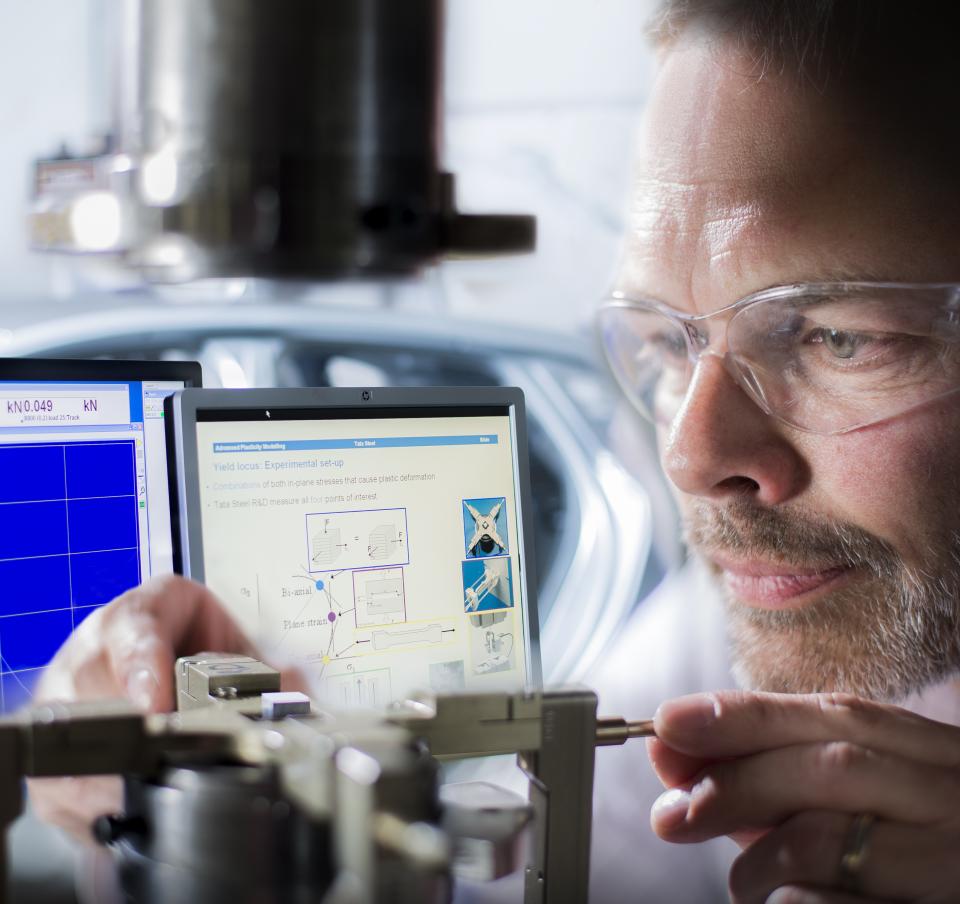
Are you interested in reducing your total cost of ownership?
Our TCO Scans identify and quantify the potential reduction in the total cost of ownership (TCO) that our advanced steels can offer your specific processes and applications. TCO Scan HyperForm can be used both on an existing part where the emphasis is on improving press shop performance, and on new parts yet to start production. We quantify the TCO benefit to your component when replacing a conventional HSS or DP grade with HyperForm grades, applying our latest tools and techniques during the different steps to support our analysis. Our renowned experts on material plasticity and our state-of-the-art material models are at your disposal, making your simulation results class-leading.
Customers who collaborated in a TCO Scan exercise were able to make clear cut decisions and successfully apply HyperForm products. We work together with our customers to calculate the actual cost/weight/performance benefit derived from the application of the HyperForm materials.
For automotive downloads such as brochures, case studies and data sheets, please click below:
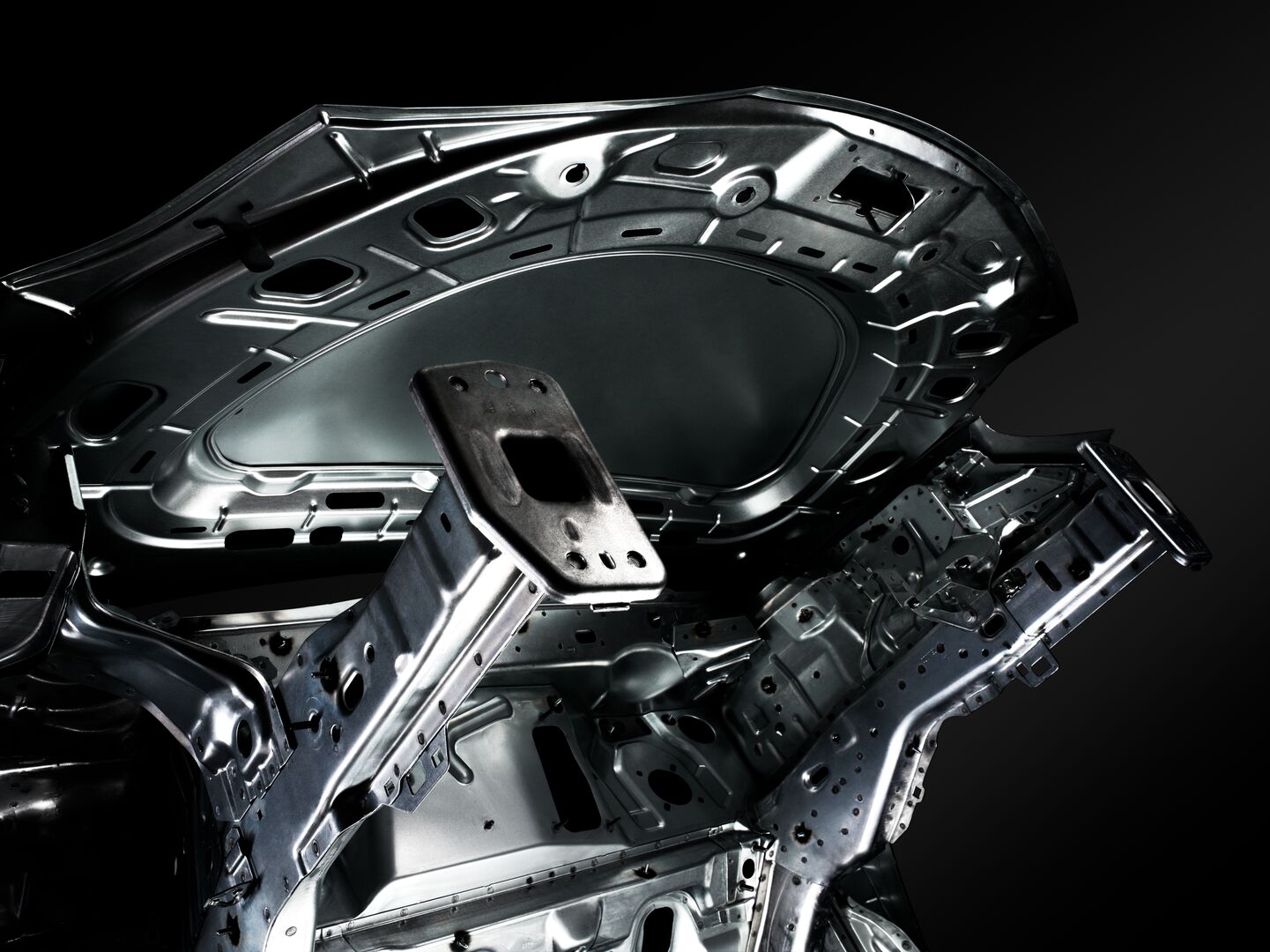