Save as much weight as possible
Tata Steel was the only steel supplier to be invited by Hyster Yale to work with the company on the next generation forklift truck series. This project include providing design and analysis advice on the latest steel products.
Tata Steel invested over two years of EVI (Early Vendor Involvement) into the project, applying the very latest in automotive engineering tools to study the chassis structure and overhead guard (OHG) of the forklifts. The resulting recommendations have been proposed for implementation in Hyster-Yale’s next generation of lift trucks.
For Hyster-Yale, this project represented a new way of working: technically literate and forward-thinking. The weight saving should result in cost savings for its customers, contributing to Hyster-Yale’s objective of offering the lowest total cost of ownership.
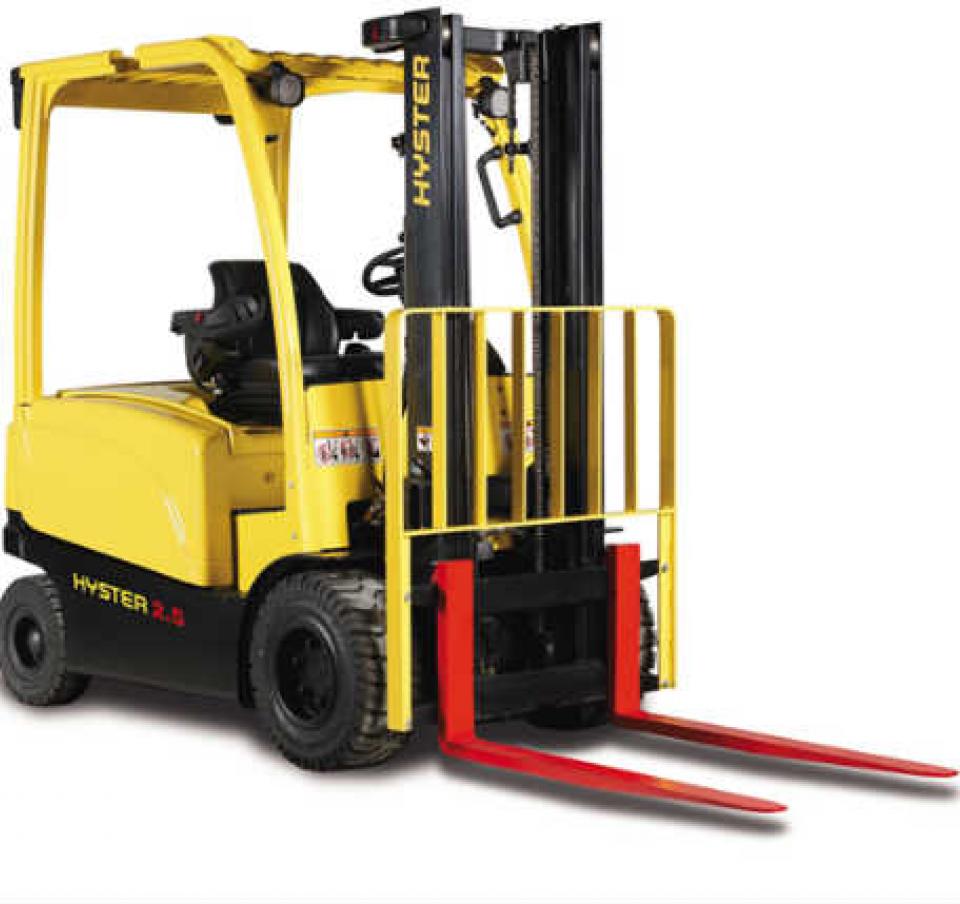
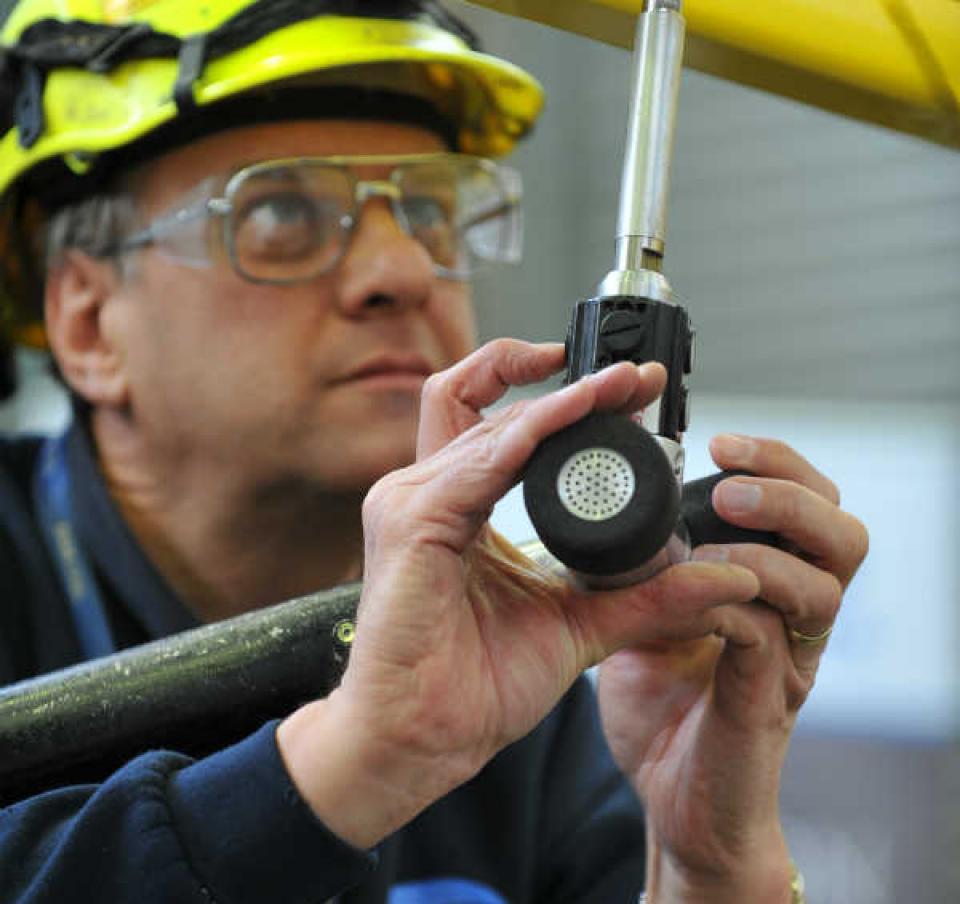
Lowering the total cost of ownership
The innovative approach from Tata Steel helped Hyster-Yale identify opportunities to deliver lower total cost of ownership to its customers.
Major weight and cost savings
Weight saving per unit of 106kg.
Innovative approach to vehicle analysis
Two EVI (Early Vendor Involvement) projects, applying the latest methods from the automotive engineering industry to look at the chassis structure and overhead guard.
Lighter chassis
New chassis design delivered 30% reduction in mass and a 20% reduction in the number of components.
Tata Steel has enjoyed a long-standing and successful relationsip with Hyster-Yale for several years. It supplies around 12,000 tonnes of hot rolled sheet steel each year. Supplying Hyster-Yale’s plants in Craigavon (UK), Nijmegen (Netherlands), Masate (Italy), Shanghai (China) and Cavite (Philippines), Tata Steel was recently awarded the Hyster-Yale award for continous improvement.
Hyster-Yale’s mission statement is to:
“Be a leading globally integrated designer, manufacturer and marketer of a complete range of high quality, application-tailored lift trucks, offering the lowest total cost of ownership, outstanding parts and service support and the best overall value.”
In line with these aspirations, it challenged Tata Steel to save as much weight (and therefore cost) as possible on its next generation forklift truck series using its EVI program.
Tata Steel examined the design of the chassis structure and the overhead guard (OHG). Initial discussions with the Chief Engineer – Advanced Concepts, at the client’s European Concept Centre, led to defining a project that would apply advanced finite element analysis (FEA) tools with a view to making the forklift chassis and overhead guard (OHG) lighter.
The designs of both elements were considered to be candidates for applying new technology.
All the product design and development is undertaken at Hyster-Yale’s Counterbalance Design Centre in Oregon, USA.
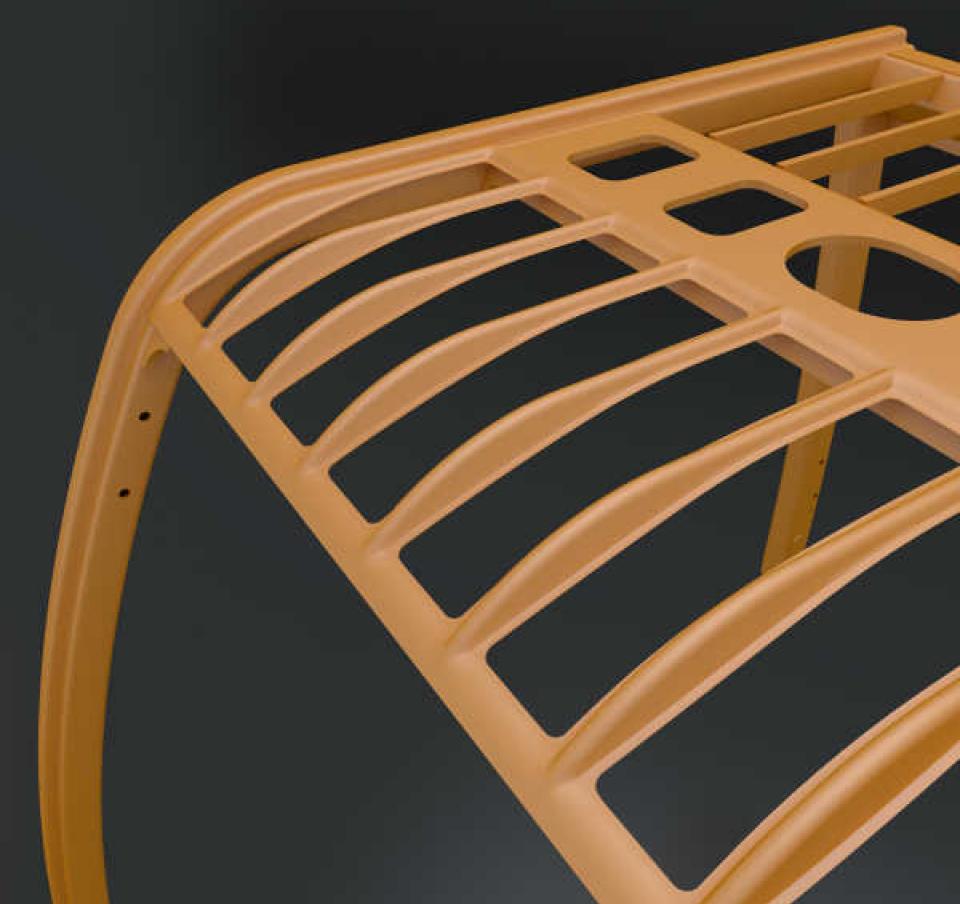
For the chassis structure
Tata Steel employed an iterative approach using a finite element analysis, with the aim of minimising mass while ensuring that structural performance was comparable with the original design. The new designs considered both the functional requirements and manufacturing cost of the components. Every attempt was made to reduce the amount of weld, with a preference for folded sheet over welded assembly in as many areas as possible.
A 3.5tn forklift chassis was analysed using ABAQUS FE software. Tata Steel then designed a new concept chassis to match the structural performance of the original design at a lower cost. During the process, 41 design iterations were completed. The result was a structure which achieved a 30% reduction in mass, and a 20% reduction in the number of components.
The lightweighting savings comprised:
- 30% potential saving
- 20% fewer components
- Comparable welding/reduced bolted joints
- All gauges comply with current Hyster-Yale supply
- Comparable torsional stiffness
- General reduction in stress levels for major loadcases; payload, 3G Battery and racking
These innovations achieved the same structural performance as before, and were recommended for implementation in Hyster-Yale’s next generation lift trucks.
For the overhead guard (OHG)
In discussions with Hyster-Yale, Tata Steel identified an opportunity to save mass and cost in the OHG by using automotive-style crash analysis to study the behaviour of the structure during the test.
The guard above the drivers’ head needs to withstand 10x impacts of a 45kg rectangular block, and must not have a residual deflection beyond the code requirements. Tata Steel modelled a 3.5tn forklift OHG using LS-DYNA software. Using this analysis, it was able to reduce the mass of the OHG by 33%, remaining within Hyster-Yale’s design requirements.
To support the OHG design changes, Tata Steel undertook a series of practical tests at its R&D facilities in the UK. Hyster-Yale supplied two OHGs, which were subjected to the 10x 45kg impact test requirements. The OHGs were heavily instrumented and the results were compared to the crash analysis. The exercise demonstrated that the analysis results were very close to the practical results, adding further credence to the mass reductions obtained in the design/analysis project.
The lightweighting savings achieved comprised:
- Potential weight saving of 33%
- 20% reduction in number of components (number of reinforcements)
- Bar profile savings considered
- Analysis correlated to OHG tests:
- Static test (50kN pull on frame) to validate modelling assumptions
- Representative dynamic impact test (10x45kg drops)
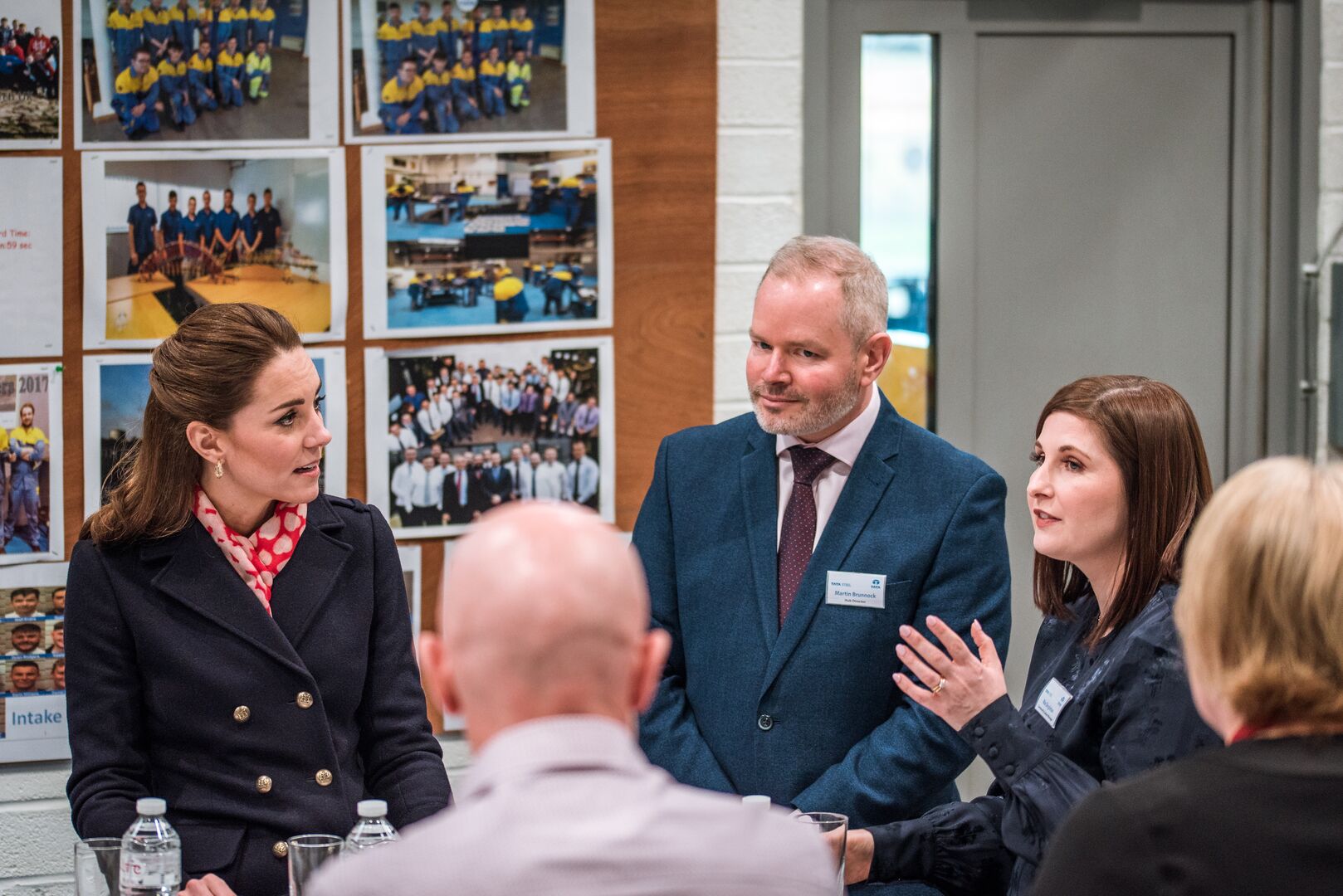