KUHN gyrotedders, which are used in the production of hay in the farming industry, are renowned for their quality of work, performance, reliability and longevity.
The gyrotedders’ arms are manufactured using high strength steel hollow sections – or tubes – supplied by Tata Steel to KUHN’s own specification. These minimise the weight of the arms without compromising performance.
Gyrotedders' arms
The arms are hinged so they can be easily folded to meet the width limitations on public roads and quickly unfolded again to work in the fields.
The hinges are cast to very precise dimensions and robot-welded onto the rectangular tube ends. It is vital that the tubes are consistent and accurate in size and shape to avoid resetting the welding robots each time a new arm is to be manufactured.
It’s also crucial that the tubes do not pose a health and safety risk, and that they help to reinforce KUHN’s premium brand positioning.
KUHN recognised that its existing tube specification needed adjusting as it was receiving too many tubes that were too concave, too convex or outside acceptable tolerances.
Tata Steel and KUHN co-developed a new high strength cold formed hollow section specification unique to this application: Hybox TT (Tight Tolerances). This specification corresponds perfectly to the design of the gyrotedders and particularly the welding process of the hinges to the tubes.
Tata Steel’s specialist sector team modified the settings of its tubes mill, which ensured the tight specifications required could be met every time.
The collaboration between KUHN and Tata Steel has improved product quality such that KUHN’s tube rejection rate is now almost zero. The need for manual re-working has been eliminated, which has boosted output yield and overall production efficiency.
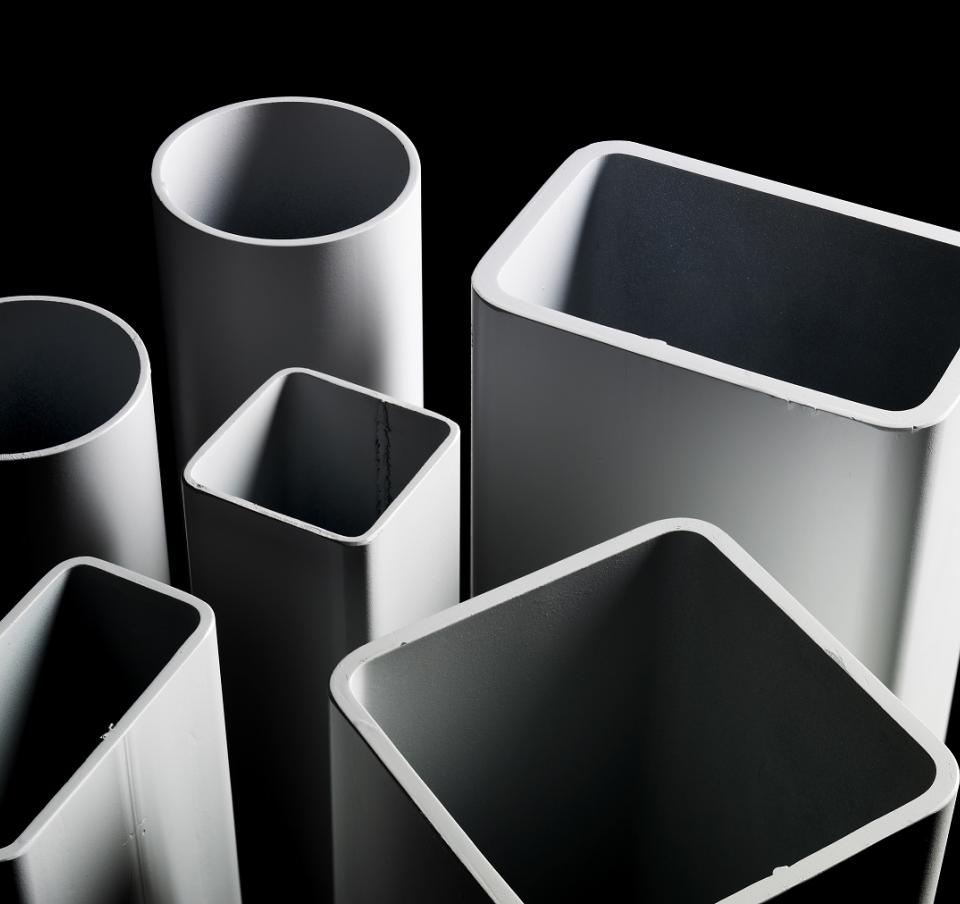
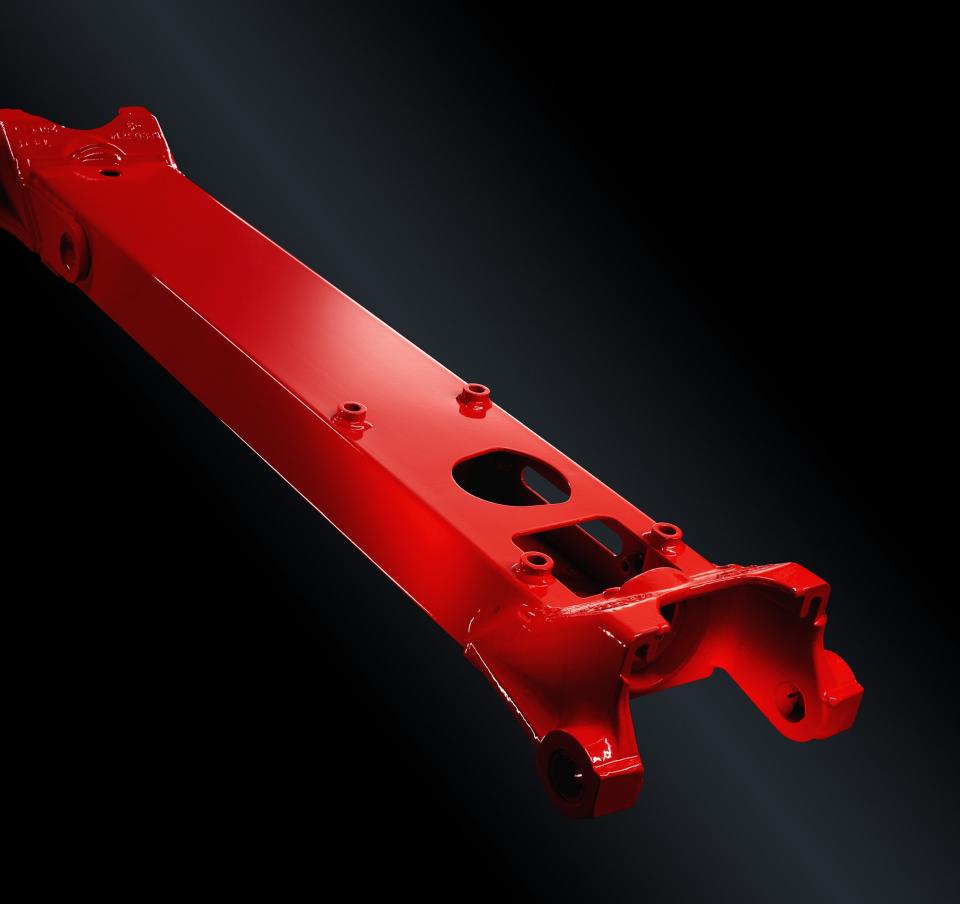
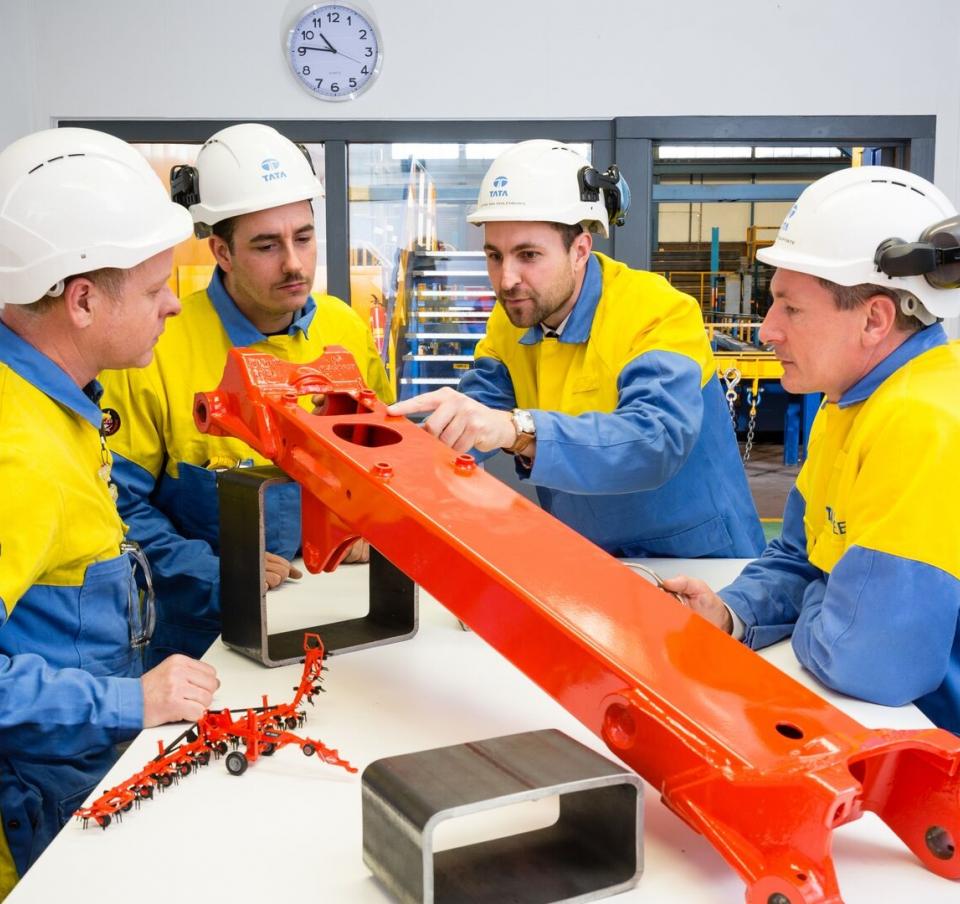
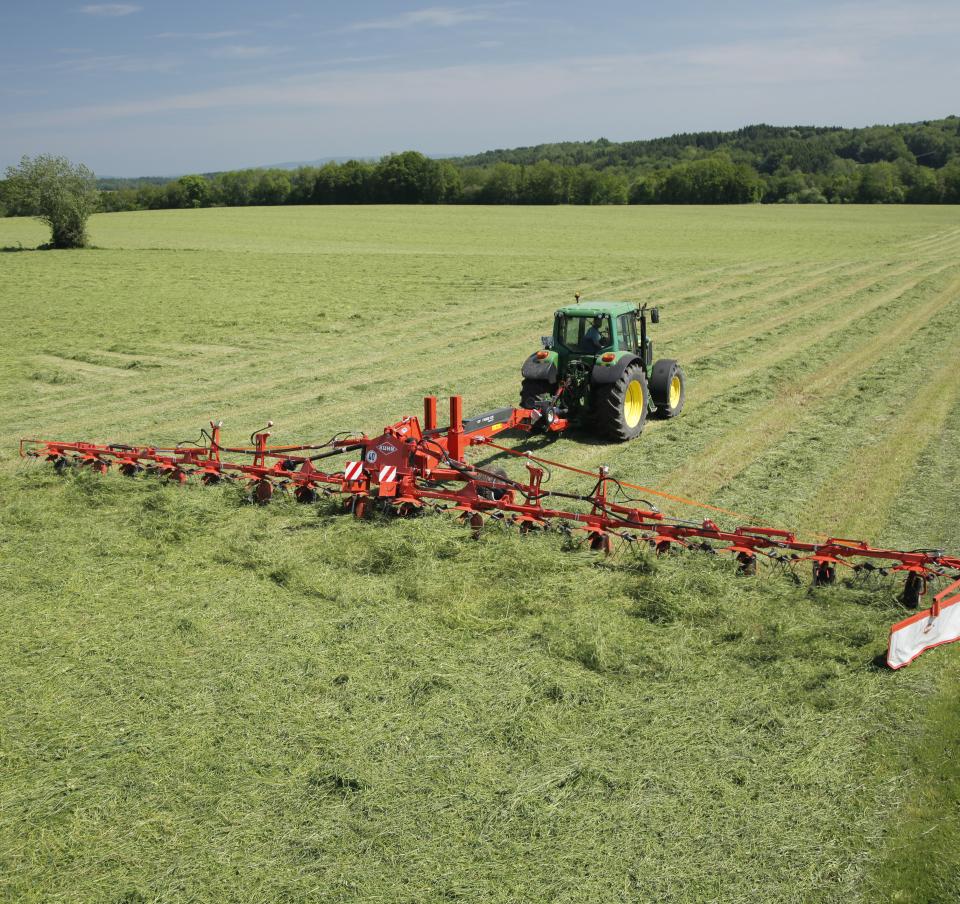
Bespoke specification
Tata Steel and Kuhn co-developed a new hollow section specification, unique to this application.
International compliance
New manufacturing specification is twice as stringent as standard EN 10219.
Zero rejection
Improved product quality and consistency mean rejection rates are now almost zero.
Health and safety first
As well as a consistent surface finish, the ends of the tubes are supplied clean, safe and free of burrs.
KUHN gyrotedders, manufactured in Saverne, France, are renowned for their high quality, durability and reliability.
Tedders are mounted or trailed machines used in the cultivation of fields to spread the crop. So they need to be able to work on hilly and uneven terrains, cover a wide area and be transported on public roads.
Minimise weight
The gyrotedders’ arms use high strength steel hollow sections – or ‘tubes’ – to minimise their weight without compromising performance.
The arms are hinged so they can be easily folded. The hinges are critical to the overall performance and longevity of the gyrotedder. Not only do they allow the arms to be folded, they also hold the transmission axles and the DIGIDRIVE® finger couplings that drive the rotors that spread the crop.
The hinges are cast to very precise dimensions and robot-welded onto the rectangular tube ends. It is vital that the tubes are consistent and accurate in size and shape to avoid resetting the welding robots each time a new arm is to be manufactured.
Concavity/Convexity
The dimensional and concavity/convexity tolerances, in particular, are very small. If the tube is too large or too convex, it does not fit into the space on the hinge. If it is too small or too concave, robot welding must be supplemented by a manual process, which incurs extra manufacturing time.
Tolerances on tube straightness are also very tight. If the section is not straight enough, the transmission axle will be put under unacceptable tension between each set of hinges.
Within KUHN’s gyrotedder range, tube wall thicknesses vary from small to large working widths. However, the same hinges are used in all the machines, so the tubes need to conform to the same specifications regardless of wall thickness.
Health and Safety
An additional consideration for KUHN is the health and safety of its employees. So it is vital that the ends of the tubes are free of burrs and sharp edges to avoid cuts during handling.
Surface Finish
The final challenge is cosmetic. Dents, scratches or rolling marks must be avoided so there is no need for heavy shot blasting or other finishing work before painting. In addition, the surface finish must be perfect, with a weld line that is extremely smooth and almost invisible. This is also a critical aspect of communicating KUHN’s premium brand positioning.
Historically, KUHN had written its own tube specifications. But it was increasingly apparent that these needed adjusting and refining because too many tubes were being rejected or reworked before use.
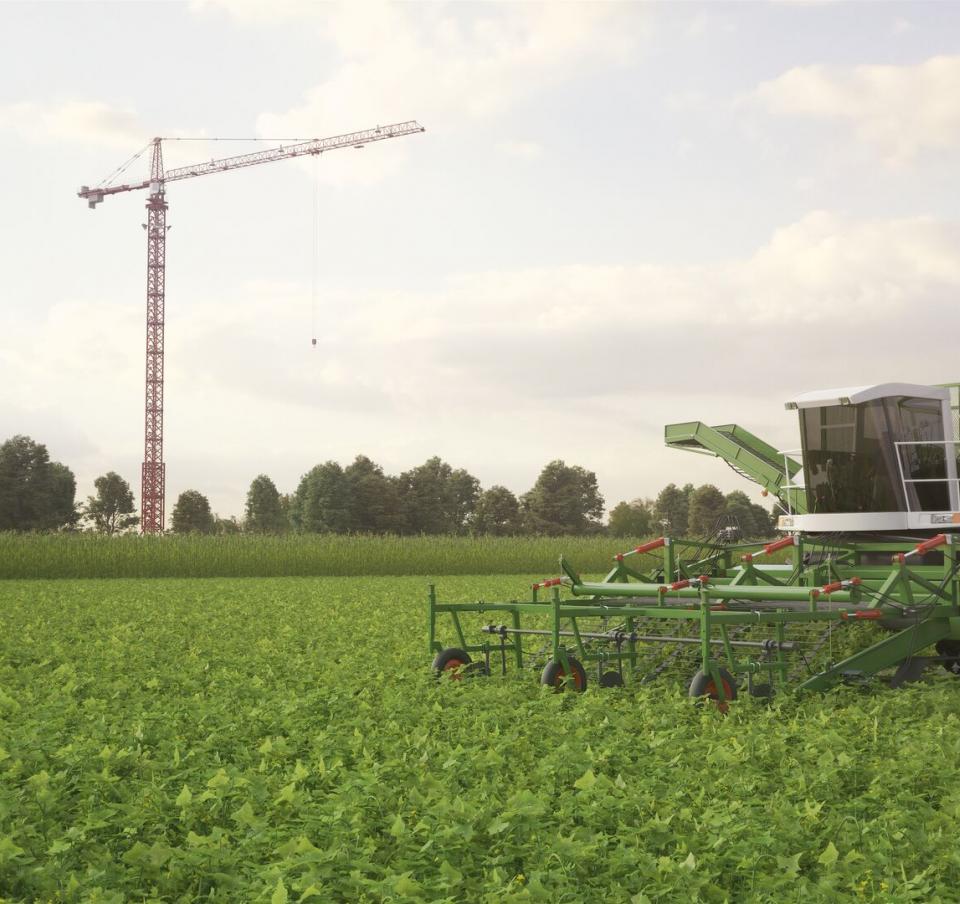
KUHN turned to Tata Steel to help improve tube consistency
Working closely together, the two partners co-developed a new hollow section specification, unique to this application. This specification corresponds perfectly to the design of the gyrotedders and particularly the welding process of the hinges to the tubes.
Tata Steel’s specialist sector team modified the settings of its tubes mill, which ensured the tight specifications required could be met every time.
Hybox TT
Tata Steel now supplies KUHN with Hybox TT (Tight Tolerances) high strength cold formed hollow sections. With a minimum strength of 355 MPa, excellent formability and weldability, it is used in a wide range of demanding construction and mechanical applications, including agricultural machinery.
The manufacturing specification for Hybox TT is twice as stringent as the requirements of standard EN 10219.
Rolled according to the precise new specifications, Hybox TT meets KUHN’s narrow dimensional tolerances and has reduced concavity/convexity values. As well as a consistent ready-to-paint surface finish, the ends of the tubes are supplied clean, safe and free of burrs. They alleviate the need to sort the tubes and reject non-compliant ones. Furthermore, they enable the smooth, continuous, automated welding process that is required for serial production.
KUHN and Tata Steel
The collaboration between KUHN and Tata Steel has improved product quality such that KUHN’s tube rejection rate is now almost zero. The need for manual re-working has been eliminated, which has boosted output yield and overall production efficiency.
These results mean that KUHN has introduced Hybox TT into more machines, making its assembly plants more efficient and optimising the quality and performance of the gyrotedders. In turn, KUHN can uphold its brand promises to customers.
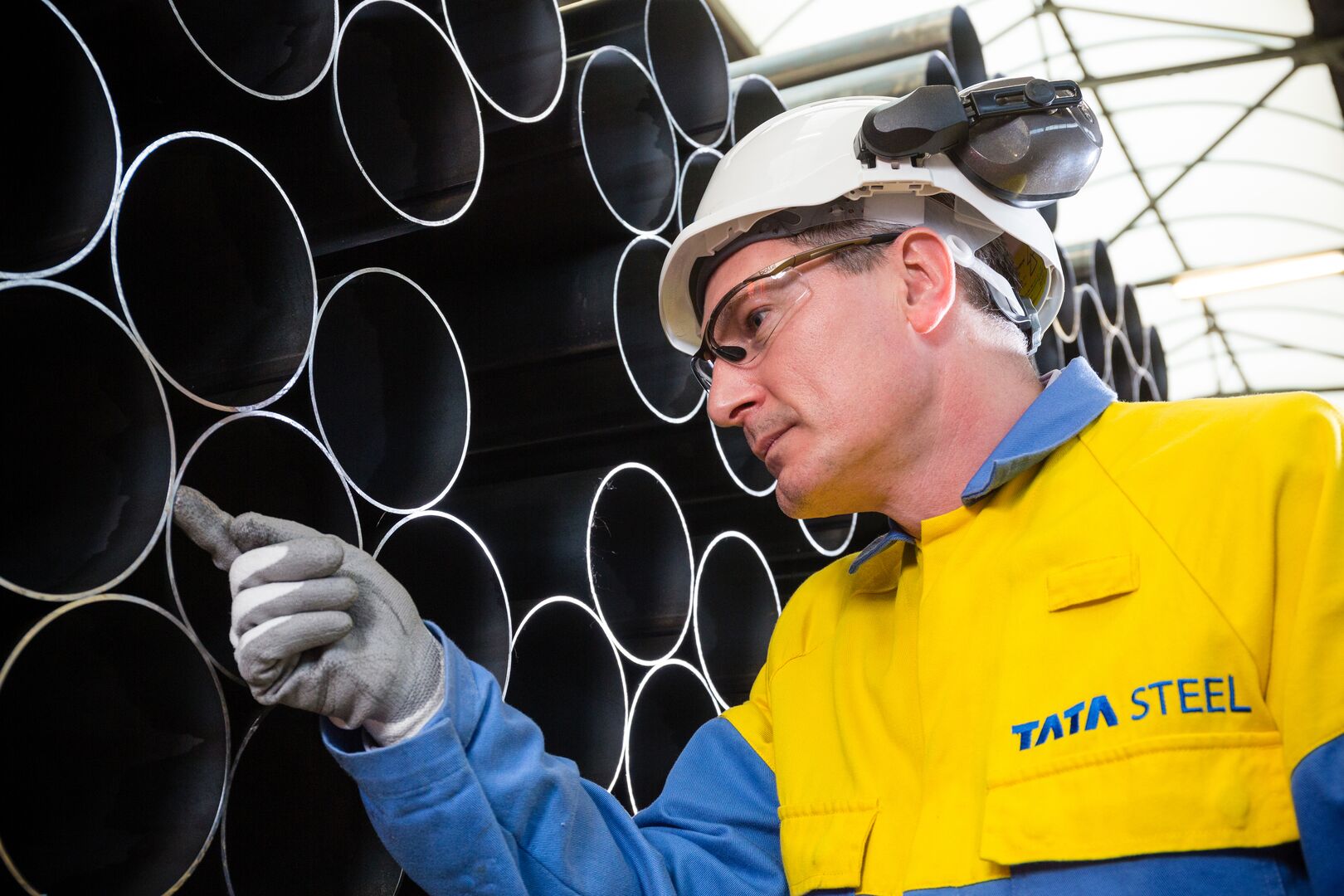