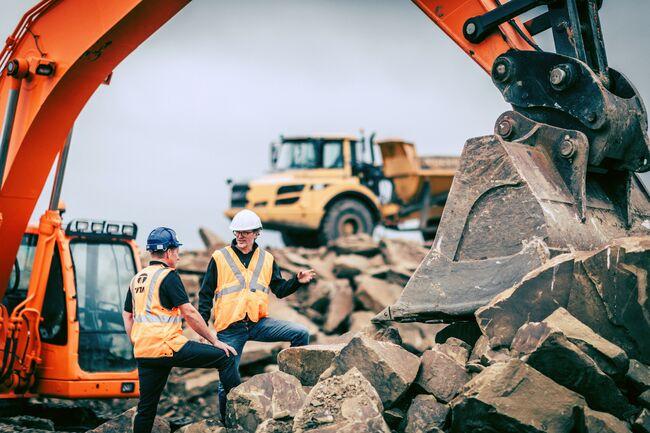
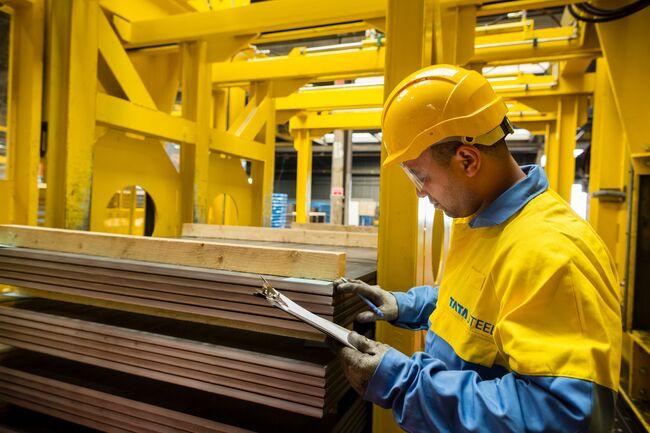
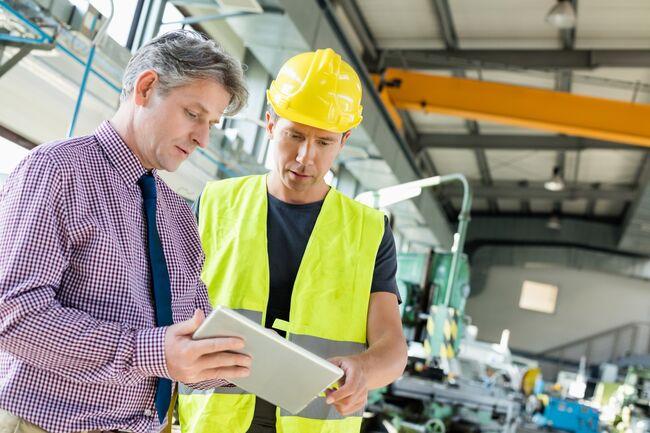
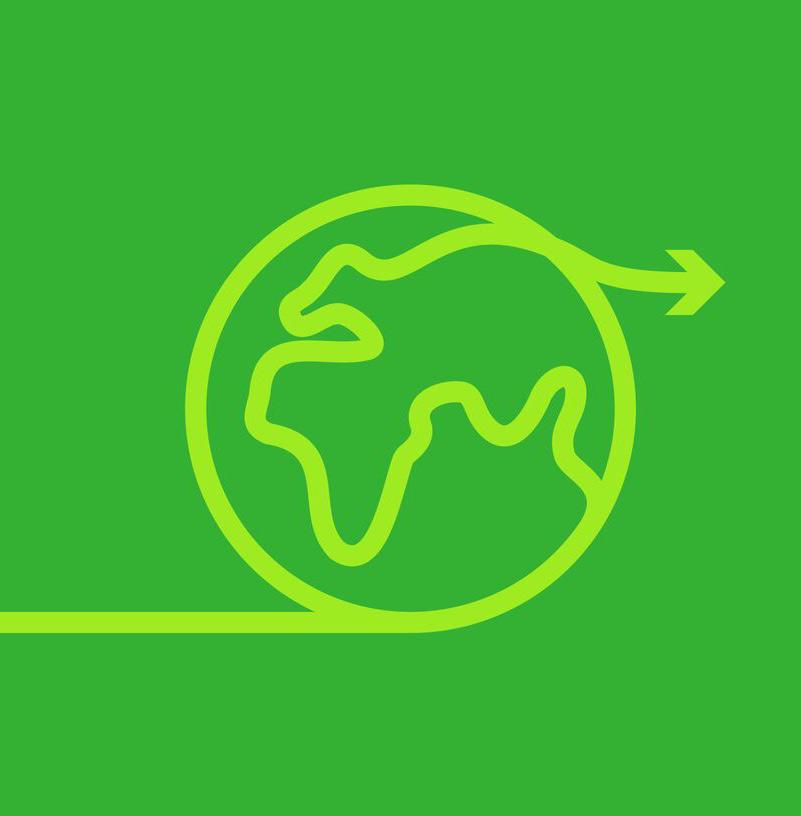
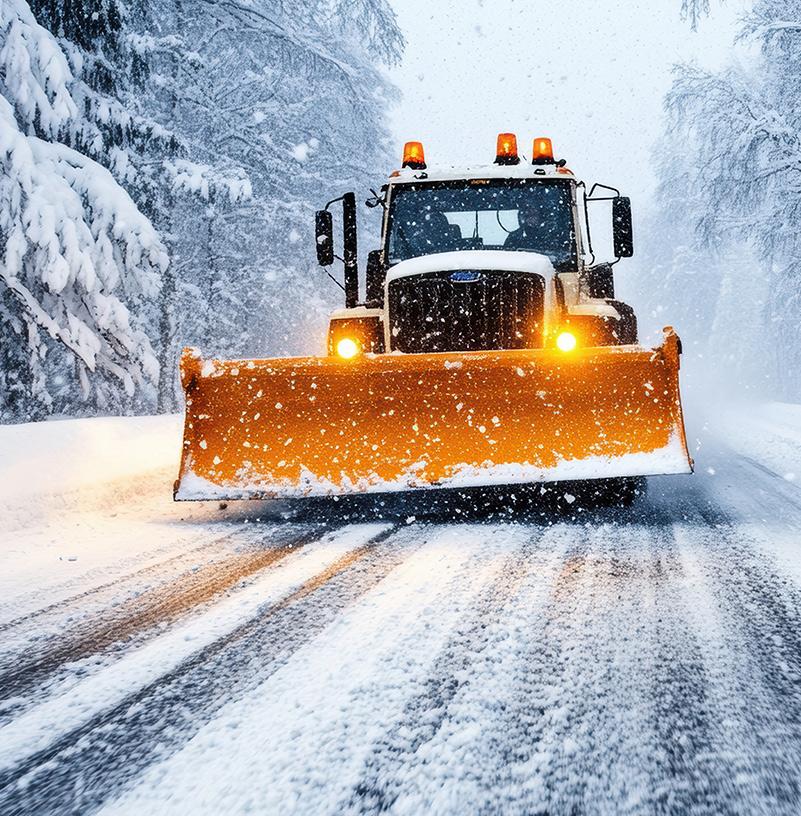


Easy processing of the toughest materials
Easy to weld
Lean chemistries ensure welding without pre-heating.
Property | Valast 400 | Valast 450 | Valast 500 |
---|---|---|---|
CEV max | 0.42 | 0.45 | 0.50 |
CET max | 0.30 | 0.33 | 0.37 |
PCM max | 0.27 | 0.32 | 0.34 |
Easy to bend
Bending under tight angles, discover the possibities:
Property | Valast 400 | Valast 450 | Valast 500 prelim |
---|---|---|---|
up to 8 mm | 3 t | 3.5 t | 4 t |
8 - 12 mm | 3.5 t | 4.5 t |
Easy and efficient laser cutting
- Benefit from the best steel strip nesting solutions.
- Stress-free over long lengths
- Produce long laser-cut parts without internal stress
Tolerances:
- 1/2 EN on gauge
- Special lengths, widths, shapes, and flatnesses upon request
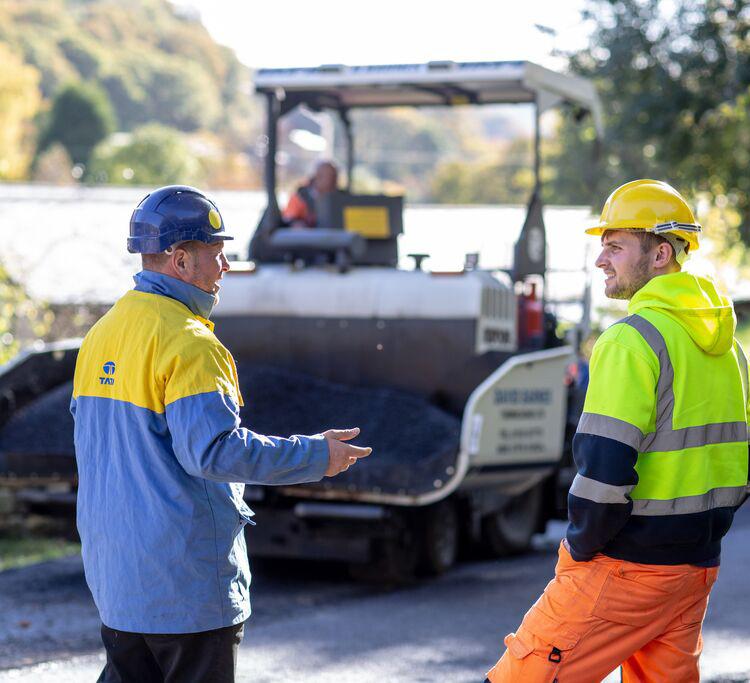
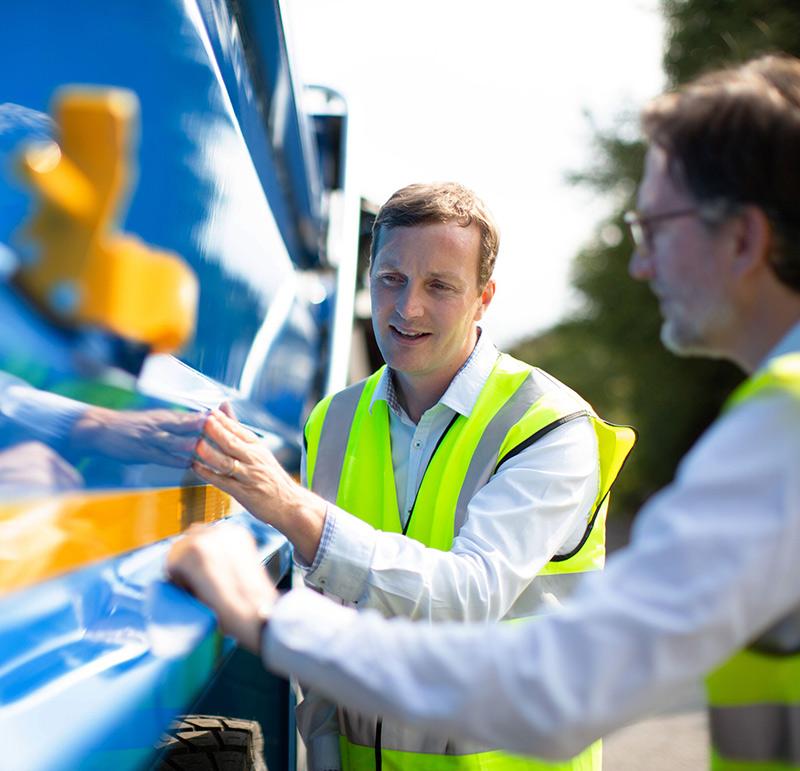
Built to last, designed to impress
The machines that operate under tough conditions, also show how professional you work. This means they must look as good as they operate.
Tata Steel's Valast combines wear resistance with great surface appearance.
Valast is ideal for paint appearance of tippers and other vehicles with long uniform surfaces.
No pre-treatments are needed to remove surface imperfections or to avoid an orange peel paint effect.
More uniform scale and no surface imperfections
Valast offers a superior surface quality thanks to the uniform scale layer. In any steelmaking process, an oxide layer forms on the surface of the steel. Wear resistant steel is often produced in reversing plate mills and cooled and hardened with water and air. This process creates a thick and uneven scale formation. In contrast, Valast is produced in a hot strip mill, which replaces the quenching method of the reversing mill process with a direct cooling method. This results in a thinner and more homogeneous scale layer. State of art decoiling ensures any remaining uneven scale is removed prior to levelling and cutting the material to its ordered length
Valast is available in 400 - 450 - 500 HB (Brinell hardness) and can be supplied to you in custom sheet lengths and with shorter lead times due to our robust local supply chain.
EN-Engineering-Brochure-Valast
Valast - Brochure
EN-Engineering-Datasheet-Valast 400
Valast 400 - Data sheet
EN-Engineering-Datasheet-Valast 450
Valast 450 - Data sheet
EN_US-engineering-data-sheet-valast-500-en-us
Valast 500 - Datasheet
EN-Engineering-Valast-Scorecard
Valast 450 Strip vs Plate - Scorecard
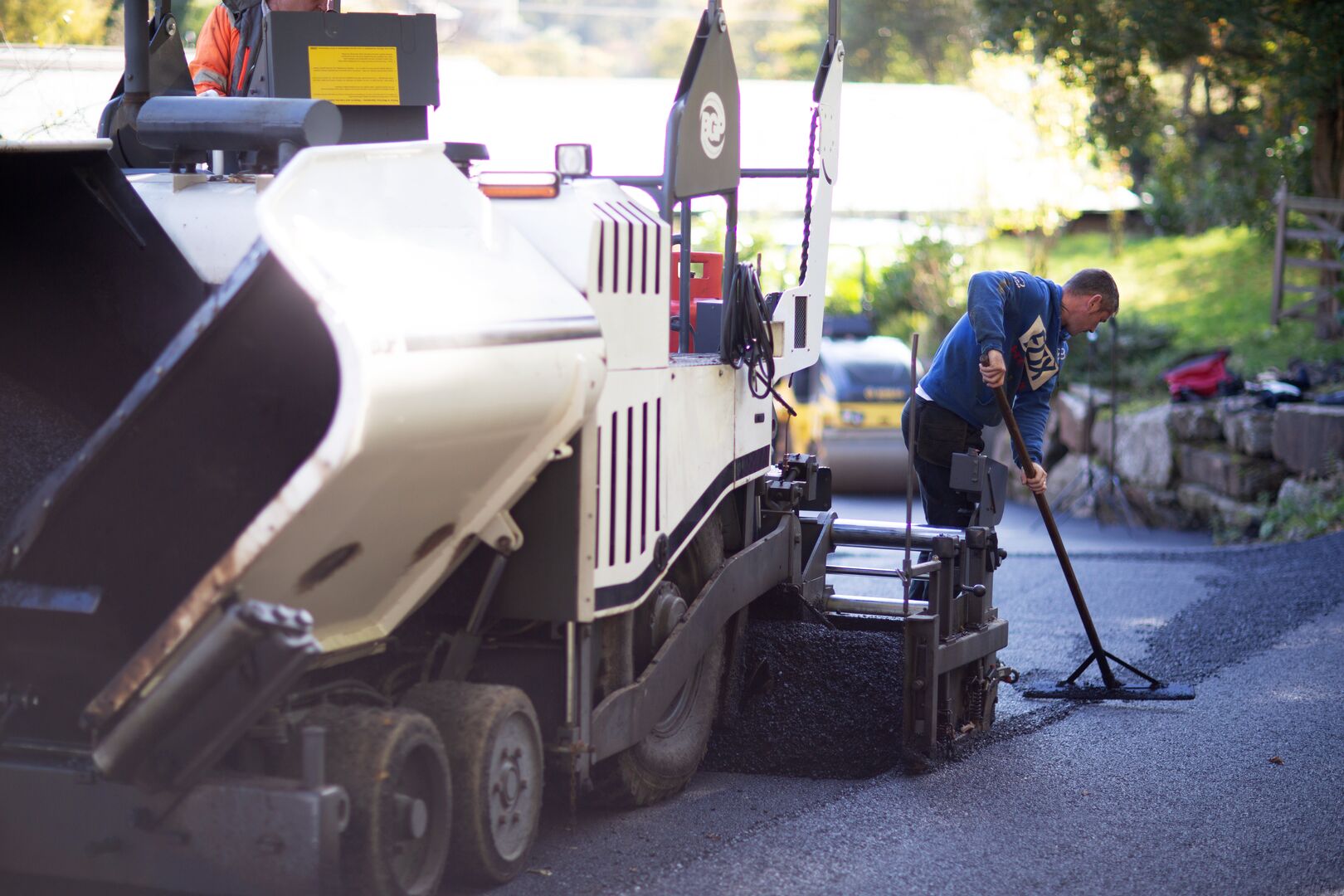