Tata Steel Europe is one of Europe's largest steel producers, and its Dutch-based Tata Steel Nederlands (TSN) Ijmuiden steel mill close to Amsterdam is one of Europe's largest steel mills.
The Ijmuiden steel plant has been investing in environmental protection for years. Numerous projects and development plans have been carried out at the mill to reduce emissions from various stages of manufacturing since the 1990s, and the results of the work can be seen today. In the annual World Steel Association (WSA) study, steel mills are valued with amount of emitted greenhouse emissions per ton of raw steel. All the world's most significant steel production facilities are included in the study. According to the latest research, the Ijmuiden steel mill is the third most efficient mill in the world in terms of emissions. The achievement is a good indication of decades of investment for a cleaner tomorrow.
However, this is not the final goal, but a new target has already been set for the future. Just slitely reducing emissions alone is not enough if we want ourselves and our children to live in a clean environment in the future. That's why we must strive for even better performances.
Ijmuiden's ambitious plan is to cut the emissions of the entire production process and distribution chain by as much as 40% by 2030 and become a completely carbon-neutral steel manufacturer by 2045. We call this journey towards a cleaner tomorrow with a name Zeremis®. The scale of the work is enormous, considering the size of the Ijmuiden mill and the diversity of the supply chains. Nevertheless, the journey has started and the implementation of the plan has begun. Action plans have been drawn up to reduce emissions at every stage, from the procurement of ore and from the steel mill to further processing operations. Results have already been obtained when e.g. the Finnish and Swedish service centers in Naantali and Halmstad were found to be carbon neutral in their own operations (scope 1&2). These service centers were Tata Steel's first carbon-neutral sites and a good indication of Nordic emission and energy efficiency.
Of course, the biggest change will take place in the steel mill itself, where two large scale blast furnaces are being used. The purpose of the Zeremis project is to change the mills production from the old blast furnace technology to the new era of steel making with green hydrogen reduction. We will move to hydrogen reduction in stages, and "green" steel products will enter the market within this decade. Finally, in the 2040s, the entire mill has gone through its great upheaval and there on produces only emission-free steel.
The journey is long, but we are already on the move.
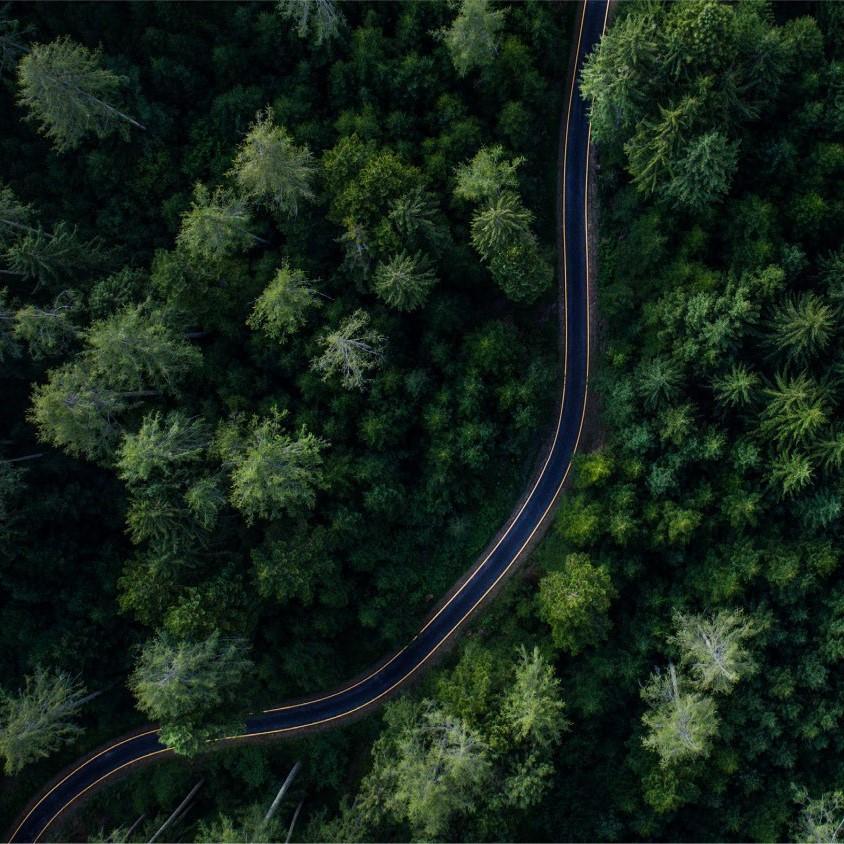
EN-Service centres-Contact-Finland Naantali
Finland - Naantali Steel Service Centre Oy
Naantali Steel Service Centre Oy
Rautakatu 5
21110 Naantali
Finland