In case you ever had the experience of driving a battery electric vehicle (BEV), chances are high that you might have thought: “this could be better”. Well, you are right, probably it could.
No, don’t mistake me that I don’t like EV’s, because I do. I think they are great and a huge improvement compared to the dirty diesel- or petrol-powered vehicles from the previous era. But looking frankly at the price, performance and looks of most of the contemporary EV’s one might not escape the thought that things could be further improved. And rightly so, they can, because EV’s are practically only in their infancy as basically the electrification of the automotive industry only took off about 15 years ago. Comparing this to the many years of development that have went in the optimisation of the traditional cars, it is not difficult to conclude that huge improvement still lies ahead of us.
At Tata Steel we practically distinguish between three different ‘waves’ of EV development, which can be roughly distinguished by the era in which they took place, the drivers behind their development and which (design) requirements were pursued. One spoiler alert: we are currently in wave 2, but the best is yet to come because wave 3 is about to start and we are excited to contribute to it.
But let me start by explaining how these waves are characterised, and then I will come back on the contribution of steel to the third wave.
Wave 1: “Meeting CO2-emission targets” ~2010 - 2018
The electrification of the automotive industry took off after 2010. The first electric vehicles that came to market were often based on a converted ICE-platform and were primarily used by the OEMs to meet their in-use, fleet-average CO2-emission targets in order to prevent penalties. To tackle range-anxiety of the consumer, range was an important design-requirement, but as mostly ‘off-the-shelve’, 1st generation technology was employed these vehicles were not very efficient and much more expensive than equivalent-sized ICE-powered vehicles.
Opel Ampera
Wave 2: “Best in-use performance” ~2018 - 2026
In the second wave of electric vehicle development, in which we see the first “EV-born” skateboard designs coming to the market, attention is paid to striking the right balance between the vehicles’ performance and the Total Cost of Ownership of the user, while legislation on in-use, fleet-average CO2-emissions are still important drivers behind the electrification of the OEM vehicle fleets. Range remains important, but driving efficiency, and also the further improvement of (battery & passenger) safety come up as new focus areas in the development of new electric vehicles. Since the OEM does not have in-house expertise on all the required technologies, partnership and in-sourcing strategies become more and more important as enablers to develop a competitive edge for the OEM.
Volkswagen ID.3
Wave 3: “Best life-cycle performance” ~2026 - 2040
In the journey of society towards carbon neutrality, the development of sustainable forms of mobility is essential, which is why OEMs have set themselves stringent targets for the complete electrification of their fleets. Towards the end of the decade electric vehicles will start to be developed based on their cradle-to-cradle environmental footprint, stimulated by legislation that will adopt life-cycle based targets, while at the same time the affordability of future forms of mobility needs to be improved. Design focus will therefore shift to efficiency, cost and through-chain sustainability, while the required range is expected to become an easy-to-achieve target for future vehicles. OEMs will increasingly take ownership of strategic technological areas that determine their competitive position, while the partnership-models remains to be important as technology continues to be further improved between subsequent EV-generations.
Steel E-motive
Okay, knowing that we are in wave 2, and moving to wave 3, what challenges lie ahead of us in achieving “Best life-cycle performance”? First of all we need to completely rethink the design of electric vehicles: taking a truly holistic approach and designing for sustainability. Lightweighting is no longer a purpose on its own but a means to an end to achieve an improved sustainability of the vehicle over its complete lifecycle. This could mean that extreme lightweighting is not required anymore and even within the steel product mix, we might see a shift back to lower strength steels, in particular if these are easier to produce on the basis of high recycled content.
A revolution like that does not happen over night and requires close collaboration between companies in the automotive value-chain. Leaving no stone unturned in reaching creative solutions for sustainability, performance and cost. At Tata Steel we are ready to embark on this journey. Steel is there to stay, but we all have to reinvent ourselves on our road to more sustainable vehicles and value-chains.
>> Return to the main Automotive blogs page
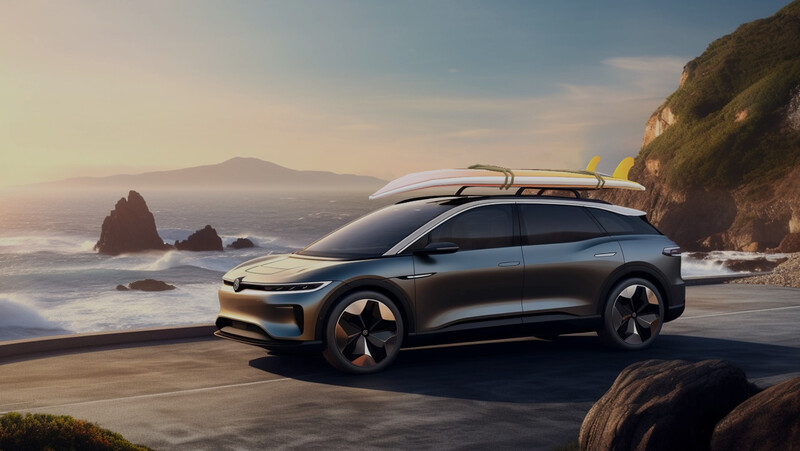