At Tata Steel Nederland we have started a series of investments to steadily increase the recycled content in our steels over the coming years, from 17.6% up to 30%.
By increasing the amount of scrap used in our production we not only significantly lower our carbon footprint but importantly also maintain the value of the scrap. By converting it into high grade steel products we prevent downcycling of this scrap which would likely happen in case it was exported to steel mills outside Europe.
Opting for steel with a higher recycled percentage, you contribute to reducing CO2e emissions and building a more sustainable future for your value chain.
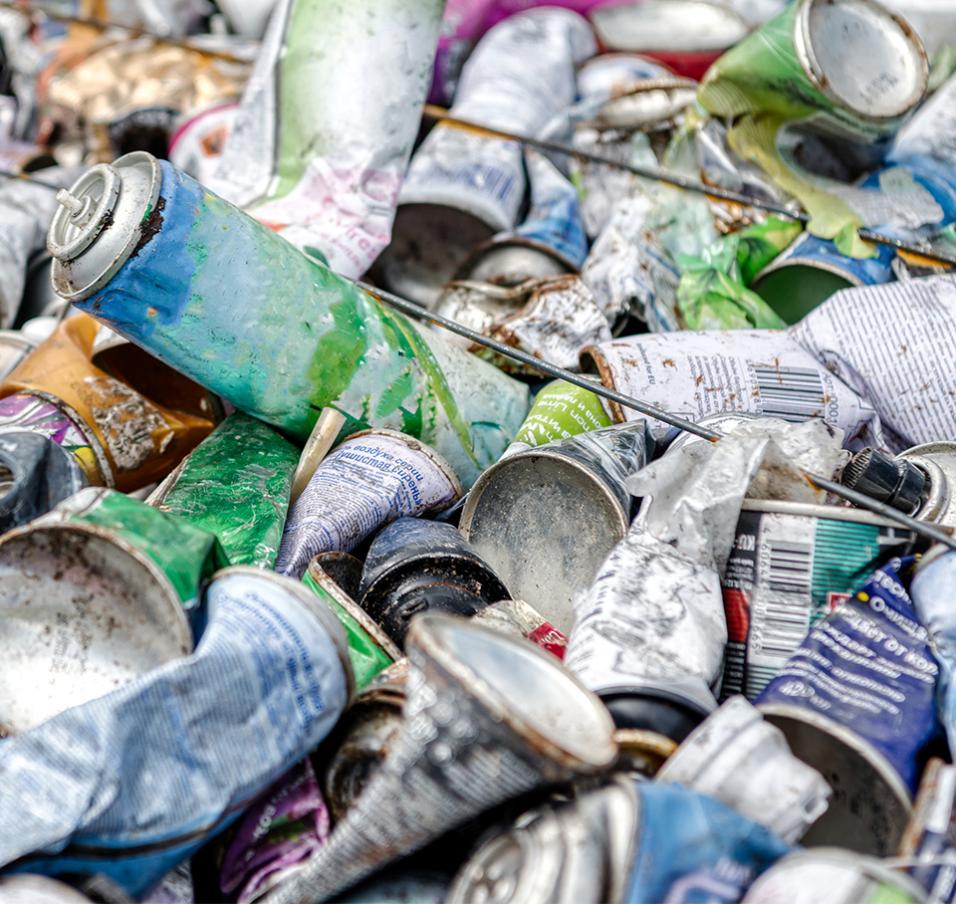
Circular steelmaking: the role of scrap in reducing CO2
In the process of steelmaking, the blast furnace is the primary source of CO2e emissions. By increasing scrap input in our steel plant, we not only contribute to circularity, but also significantly reduce the need for molten iron production. This directly lowers CO2e emissions. We estimate that for every tonne of additional scrap input, we avoid using 1.6 tonnes of virgin iron ore and roughly 500 kg of mined coal. This results in a CO2e reduction of 1.6 tonnes, as reported by World Steel Association.
Improved scrap infrastructure
To manage this effectively, we are making numerous investments such as building additional scrap warehouses and expansion of our scrap related logistic capabilities (such as cranes to load ships and trains) both internal and for sourcing additional external scrap. This helps reduce the amount of scrap exported outside of Europe, where it is often downcycled into lower-grade applications such as concrete rebar. To avoid losing high-quality alloys, it is crucial to recycle rather than downcycle.
Extensive testing
Moreover, we started extensive research and testing to gain a complete understanding of how a higher scrap content in our final products affects the quality of our steel and the limitations of our current setup. Our initial trials successfully tested the impact of unintended metallic elements, known as tramp elements, in scrap. The results were positive, indicating that we can effectively control the adverse impact of tramp elements, although we still need to further improve on this.
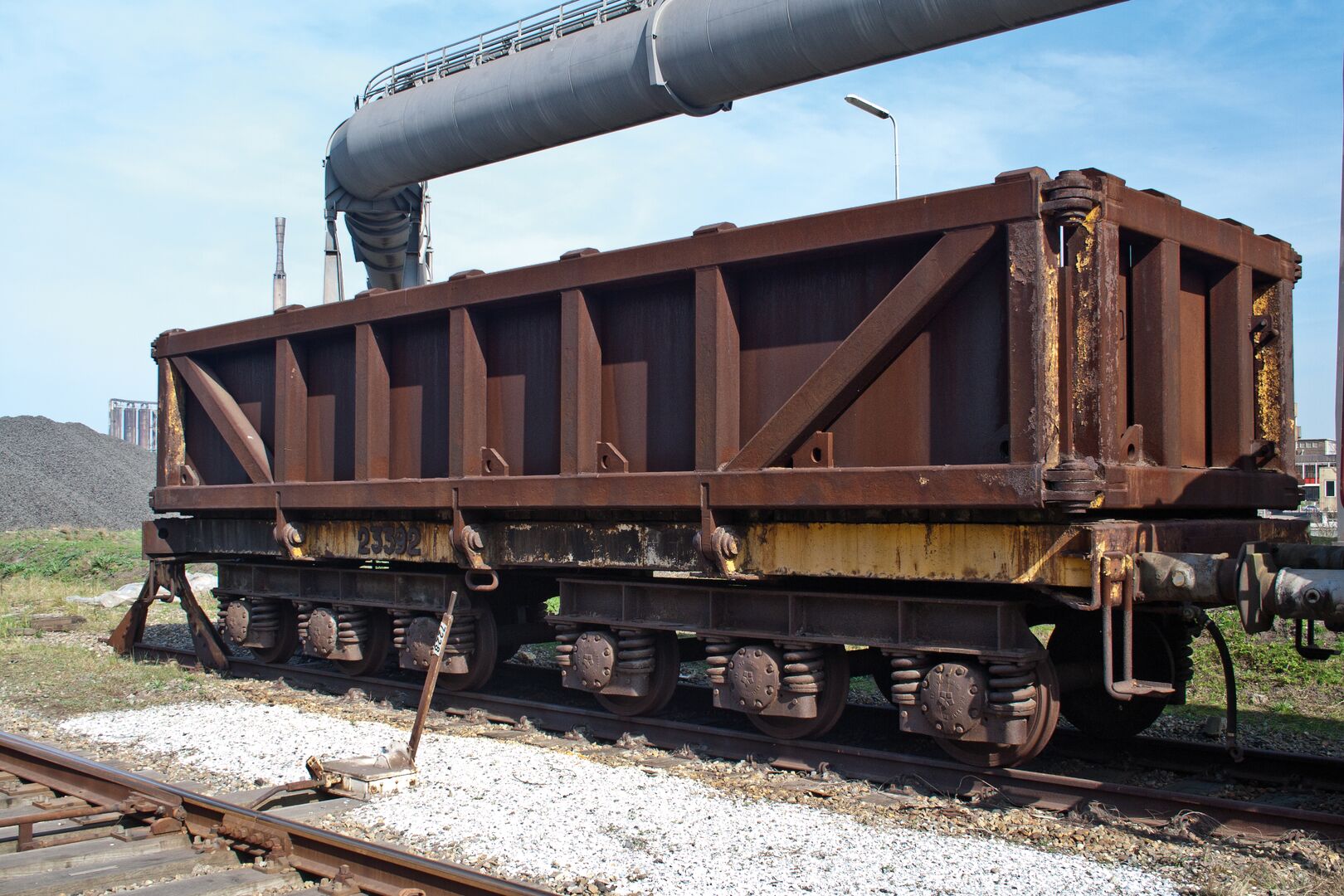
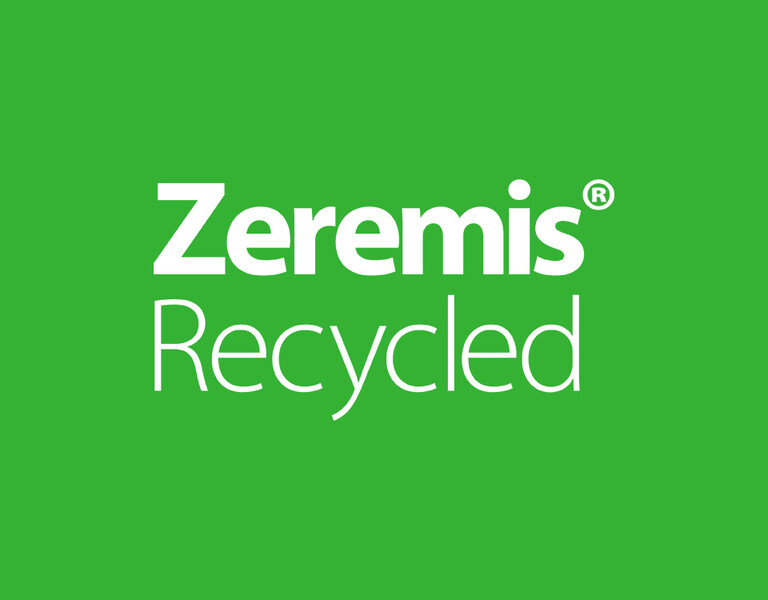
Gradually increasing scrap rate
We are now ready to introduce these improvements and gradually increase the scrap rate the coming years, ensuring a continuous stream of carbon savings. Under the name Zeremis Recycled, we already offer our customers a product with an improved recycled content rate of 30% in a mass-balanced way. The revenues generated from this initiative are used to accelerate our transition towards carbon-neutral and circular steel making.
Up next
With our new way of steelmaking via DRI and EAF we will deliver 30% recycled content in 2030. Meanwhile we will continue to increase our recycling rate to the technical limits of our current configuration.
Recycling milestone: 120 million kg of old tin by 2026
Tata Steel Nederland is taking a major step toward a circular future by aiming to recycle 120 million kilograms of old tin by 2026. Learn how this ambitious goal supports our sustainability strategy and contributes to reducing raw material use and CO₂ emissions.
AI and laser technology boost steel recycling
Tata Steel Nederland is using high-tech laser systems and artificial intelligence to take steel recycling to the next level. Discover how these innovations improve scrap sorting and help recover more high-quality steel from used materials.
EN-Corporate-Contact-Sustainability-Zeremis Carbon Lite
Contact your account manager or mail to:
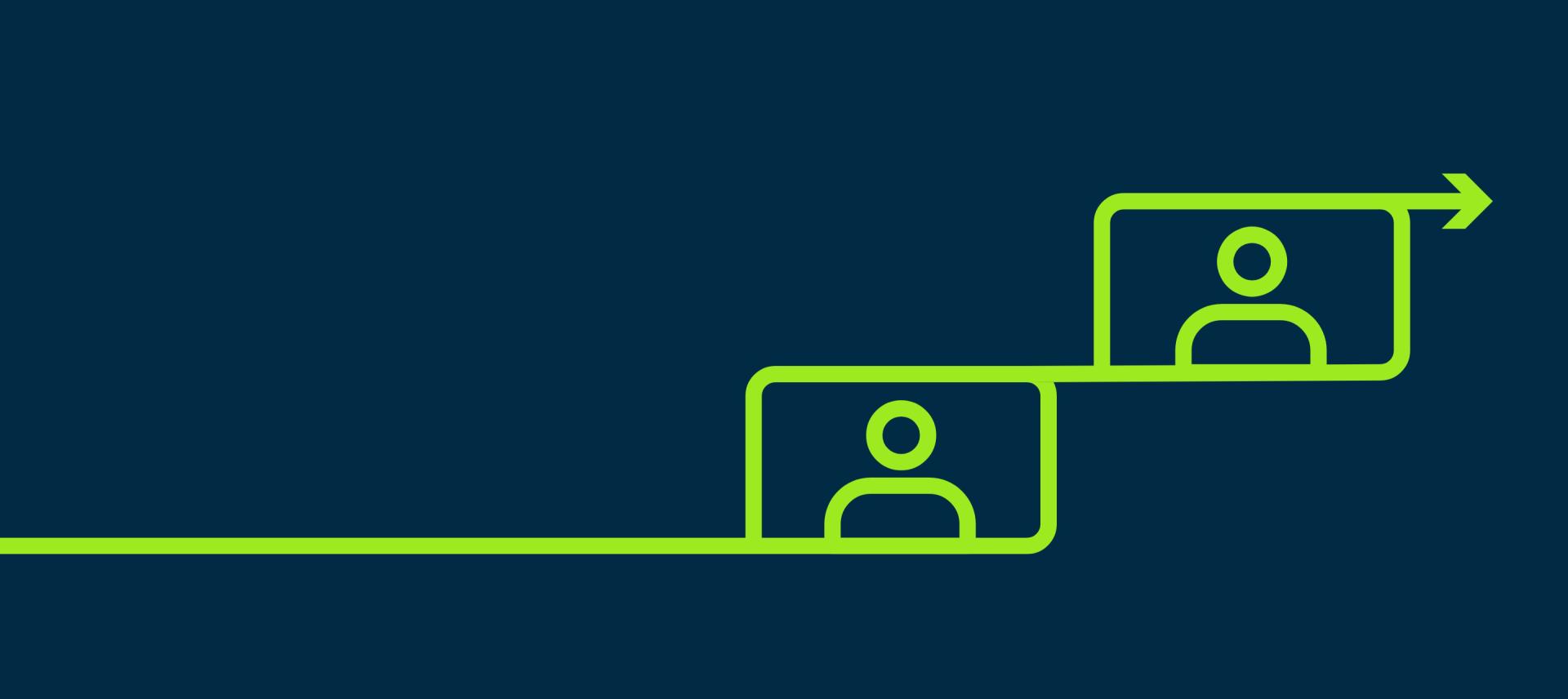